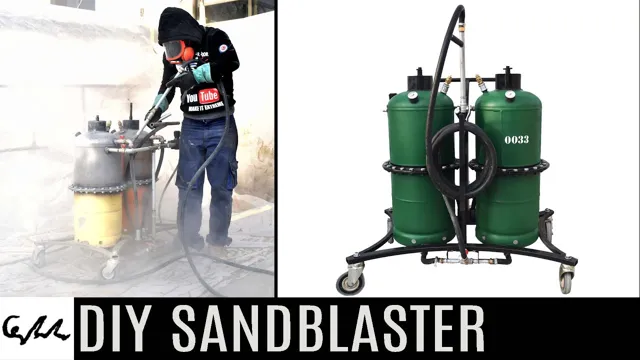
Have you ever needed to do some serious cleaning on a tough surface but didn’t want to spend a fortune on specialized equipment? Well, look no further than a homemade sandblaster! And even better, you can make one with just an air compressor and a few other materials. Sandblasters work by using a high-pressure stream of sand to strip paint, rust, and grime off of surfaces. With the right setup, you can even etch designs into glass or stone! And while store-bought sandblasters can be costly, making your own can be a fun and affordable way to get the job done.
In this blog post, we’ll walk you through the steps to make your own sandblaster using an air compressor. From the materials and tools you’ll need to the actual assembly and operation of the setup, we’ve got you covered. Plus, we’ll throw in a few tips and tricks to help you get the most out of your homemade sandblaster.
So if you’re ready to tackle tough cleaning jobs or get creative with your own designs, read on to learn how to make a sandblaster with an air compressor!
Introduction
Are you tired of trying to clean surfaces with traditional methods? Making a sandblaster with an air compressor can be a cost-effective and efficient solution. A sandblaster works by shooting a high-powered stream of sand at the surface you want to clean, making it perfect for tough and stubborn dirt and grime. To make a sandblaster with an air compressor, you will need a few equipment pieces, such as a sandblaster attachment, a compressor, and sand.
Sandblasting can be quite messy, but the results are usually impressive. With a little practice and some patience, you can achieve the look of a professional cleaning service without having to spend a fortune. So why not give it a try today? Your surfaces will thank you for it!
What is a Sandblaster?
Sandblasting is a common technique used in various industries, such as construction, auto restoration, and metalworking. A sandblaster is a tool that uses compressed air to blast abrasive material (such as sand, glass beads, or walnut shells) at high speed to remove paint, rust, or other coatings from surfaces. Using a sandblaster can save time and labor compared to traditional methods of surface preparation, such as manual sanding or chemical stripping.
It can also provide a more even and uniform surface for painting or coating. However, sandblasting requires proper training and safety precautions, as the abrasive materials and debris can pose a risk of injury or inhalation of harmful particles. It is important to wear appropriate protective gear, such as goggles, respirators, and gloves, when operating a sandblaster.
Overall, a sandblaster can be a useful tool for surface preparation and restoration, but it should be used with caution and proper safety measures to ensure a safe and effective outcome.
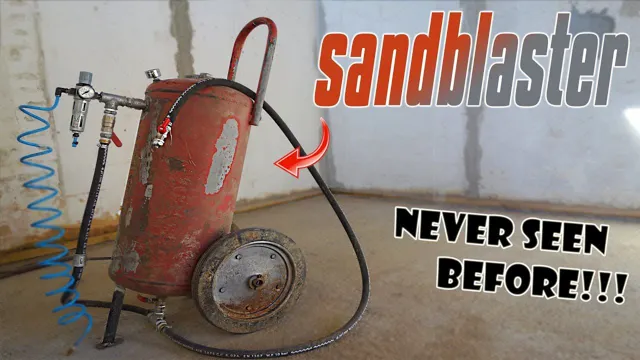
Why Make Your Own Sandblaster?
Making your own sandblaster is a great way to save money on expensive equipment while still having all the benefits of sandblasting at your fingertips. A sandblaster is a tool that is used to strip away paint, rust, and other unwanted materials from metal, concrete, or other surfaces. It is a powerful machine that can make quick work of tough projects.
With a DIY sandblaster, you can customize the design to fit your needs and budget, and have the satisfaction of knowing that you built it yourself. Plus, by doing it yourself, you have a greater understanding of how the tool works and can troubleshoot any issues that may arise. So why not take the leap and make your own sandblaster? It’s easier than you think!
Materials Needed
If you’re looking to make a sandblaster with an air compressor, there are a few key materials you’ll need to get started. First and foremost, you’ll need an air compressor capable of delivering at least 90 PSI of pressure. This will provide the force needed to propel the sand particles out of the nozzle and onto the surface you’re blasting.
You’ll also need a sandblasting nozzle, which can either be purchased or made at home using PVC piping and a few other common materials. Additionally, you’ll need sand or another abrasive material to use as the blasting media, as well as a container to hold it in and a way to feed it into the nozzle. Other materials that may be useful include a pressure gauge to monitor your compressor’s output, safety equipment such as goggles and a respirator to protect your eyes and lungs from the blasting material, and a tarp or other protective covering to prevent the sand from scattering and causing damage to nearby surfaces.
With these materials in hand, you’ll be well on your way to creating your own sandblaster with an air compressor.
Air Compressor
If you are planning to get an air compressor, you will need a few materials to make the best use of it. Firstly, you will need an air hose to connect the compressor to the device you want to operate. The hose should be compatible with the compressor you purchased.
You might also need an air filter to prevent dirt and debris from entering the compressor. Furthermore, if you are planning to use the compressor for painting or spray coating, you will need a gravity feed spray gun, a spray gun holder, and a regulator. The regulator will help you to control the air pressure at which the spray gun operates, allowing you to achieve a professional finish every time.
Finally, you should also consider getting safety goggles, earplugs, and a dust mask to protect yourself from the loud noise and airborne particles produced by the compressor. With these materials, you can make the most of your air compressor and enjoy its benefits to the fullest.
Sandblasting Gun
If you’re planning on sandblasting any object or surface at home, you’ll need a sandblasting gun. To use this tool, you’ll require a few materials. First and foremost, a compressor is necessary to deliver air to the gun and bring forth the sandblasting force.
You’ll also need a tank for storing the abrasive material, which can be anything from sand to glass beads. Additionally, you may require extra nozzles and hoses to connect the compressor to the gun. It’s important to choose the right materials that are compatible with the gun you’ve selected and the type of sandblasting you’re planning on doing.
By doing so, you’ll achieve optimal results without risking damage or safety hazards. So, before you start sandblasting, make sure you have all the necessary materials you need to get the job done efficiently and safely.
Hose and Fittings
When it comes to selecting hose and fittings for your equipment or machinery, it is important to consider the specific materials needed for your application. The type of materials used will depend on the type of fluid or gas being transported, as well as the pressure and temperature requirements. For example, if you are working with corrosive fluids or gases, you may need to select fittings made from materials such as stainless steel, brass, or plastic to avoid damage or leaks.
Similarly, hoses made from materials such as EPDM, silicone, or PTFE may be required for high-temperature applications or those involving harsh chemicals. Properly selecting the materials needed for your hose and fittings will help to ensure that they perform reliably and safely under the specific conditions in which they are used.
Safety Equipment
When it comes to safety equipment, there are several materials that you need to have on hand to ensure that you and your team are safe. First and foremost, ear protection is crucial for anyone working with loud machinery or in areas with high decibel levels. Earplugs or earmuffs can help prevent hearing damage and should be worn at all times.
Additionally, protective eyewear is essential for individuals working with flying debris or hazardous chemicals. Make sure that glasses or goggles fit properly and are free from scratches or cracks. Gloves are another important piece of safety equipment, as they can protect your hands from cuts, burns, or chemical exposure.
Be sure to choose gloves that are appropriate for your specific task and replace them if they become damaged or torn. Finally, respiratory protection is necessary for anyone working in areas with poor ventilation or hazardous dusts. Respirators can filter out harmful particles and prevent lung damage.
So if you’re working in an environment with potential hazards, always make sure you have the right safety equipment on hand.
Building the Sandblaster
Sandblasting is a popular technique for removing rust, paint, and other surface contaminants from metal surfaces. But did you know that you can easily make your own sandblaster using an air compressor? It’s a cost-effective and efficient way to get the job done. Here’s how to make a sandblaster with an air compressor: First, you’ll need to get a few supplies.
You’ll need an air compressor with a minimum of 6 cubic feet per minute (CFM), a sandblasting gun, abrasive sand, a dust mask, and safety glasses. Once you have all your supplies, you can start putting together your sandblaster. Attach the sandblasting gun to the air compressor using a hose.
Fill the gun with the abrasive sand, making sure not to overfill it. Put on your dust mask and safety glasses, then turn on the compressor. Once it reaches the desired pressure, aim the gun at the surface you want to clean and pull the trigger.
Remember to keep the gun moving at all times to avoid creating divots or uneven surfaces, and make sure to sandblast in a well-ventilated area away from people and pets. With some practice, you’ll be able to use your homemade sandblaster to tackle any metal surface. So why not give it a try today?
Step 1: Connect the Hose and Fittings
Building a sandblaster is a great DIY project, but before you can start blasting away at rust and grime, you need to connect the hose and fittings. The first step is to find a suitable spot to set up your sandblasting rig. You’ll need a compressor that can deliver at least 90 psi of air pressure, a sandblaster gun, a hose that can handle the pressure, and the appropriate fittings to connect everything together.
Once you have all your equipment, it’s time to start the assembly process. Begin by screwing the hose onto the sandblasting gun, making sure it’s tightened securely. Then attach the other end of the hose to the compressor using the correct fittings.
Don’t forget to add Teflon tape to the threads to prevent any air leaks. Once everything is connected, test out your sandblaster to make sure it’s working properly. With the hose and fittings in place, you’re ready to start blasting away at stubborn dirt and grime.
Step 2: Attach Sandblasting Gun
To build a sandblaster, the next step after assembling the air compressor and tank is to attach the sandblasting gun. First, attach the air hose to the bottom of the gun and secure it with a hose clamp. Then, connect the nozzle to the top of the gun by screwing it into place.
Ensure a tight and secure seal to prevent any leakage or loss of pressure. This step is crucial as the gun is responsible for blasting the sand onto the surface being treated. A well-assembled gun ensures the right amount of sand is dispensed, making the sandblasting process efficient and effective.
Once the gun is securely attached, the sandblaster is ready for use. Keep in mind to wear protective gear such as gloves and goggles during the sandblasting process to prevent any injuries. With the gun securely attached and all safety precautions in place, you can now enjoy creating a professionally treated surface using your newly built sandblaster.
Step 3: Connect to Air Compressor
To complete the construction of your DIY sandblaster, the third and final step is to connect it to an air compressor. This requires the installation of a compressed air line and an air regulator. It is essential to ensure that the air compressor is compatible with the sandblaster’s requirements.
You need to consider the compressor’s CFM (cubic feet per minute) and PSI (pounds per square inch) ratings. If the compressor’s CFM is too low, it won’t provide enough air pressure to operate the sandblaster efficiently. If the PSI is too high, you risk damaging the blaster.
Connect the air line using brass fittings to avoid rust and ensure longevity. The air regulator allows you to adjust the air pressure to the sandblaster. Be sure to read the instruction manual of both the compressor and sandblaster before connecting them to avoid any damage or malfunction.
Once the air regulator and line are connected, test the sandblaster’s function with a small project to ensure it is working correctly. Congratulations, you have successfully built your own sandblaster!
Safety Precautions
If you’re wondering how to make a sandblaster with an air compressor, there are a few things you need to consider to ensure both safety and effectiveness. First and foremost, it is crucial to wear the proper safety equipment, such as a respirator mask, safety goggles, and gloves, to protect yourself from the dust and debris that will be created during the sandblasting process. Additionally, you should ensure that you are using the correct type of sand, as certain types can be harmful if ingested or inhaled.
In terms of the actual process, it is important to adjust the air pressure of the compressor to a safe level, and to always point the sandblaster away from yourself and others. With these safety precautions in mind, you can successfully create a sandblaster with an air compressor and achieve your desired results.
Wear Protective Equipment
When it comes to safety precautions, one of the most important things you can do is wear protective equipment. This includes items such as helmets, gloves, goggles, and masks. Whether you’re working with heavy machinery or handling hazardous materials, protective equipment can help prevent serious injury or illness.
Not only does it provide a physical barrier between you and potential harm, but it can also give you peace of mind and confidence to do your job safely. Think of it like armor โ it may not be the most comfortable or stylish option, but it can save your life in a dangerous situation. So, don’t take any chances โ always prioritize your safety by wearing the appropriate protective equipment for your job or activity.
Remember, it’s much better to be safe than sorry.
Work in a Well-Ventilated Area
When it comes to working with different tools and equipment, it’s always important to keep safety in mind. One of the most critical safety precautions to take is making sure that you work in a well-ventilated area. Adequate ventilation is essential to ensuring that you’re not exposed to harmful fumes, dust, or other toxic elements that can lead to respiratory problems, headaches, and even long-term health issues.
If you’re working in a space that doesn’t have proper ventilation, it’s important to take steps to improve it before you start working. This might involve opening windows, using fans or air purifiers, or even adding ventilation systems to your workspace. By taking the time to ensure that you and your workspace are properly ventilated, you’ll reduce your risk of injury and maintain a safe and healthy work environment.
Remember, your health and well-being should always be your top priority!
Read and Follow Instructions Carefully
When it comes to working with dangerous tools or equipment, following safety precautions is crucial to protecting yourself and those around you. It might seem like a hassle to read instruction manuals and take additional safety measures, but it’s essential to ensure that no accidents occur. Taking shortcuts or assuming that you know how to use a tool without proper instruction can lead to serious injuries or even fatalities.
Before starting any job, always make sure to read the instructions carefully and follow any recommended safety procedures. It’s also important to wear protective gear such as helmets, goggles, and gloves, and never hesitate to ask for help or guidance if you’re unsure about how to proceed. Remember, taking a few extra minutes to review instructions and take necessary precautions can prevent accidents and keep everyone safe.
Conclusion
And there you have it, folks! With just a few tools and a whole lot of grit (pun intended), you can make your own sandblaster using an air compressor. This DIY project is a great way to save some money and have a blasting good time. So go ahead and give it a shot, but be careful not to get sand in your eyes – safety goggles are a must! Happy blasting!”
FAQs
What materials are needed to make a sandblaster with an air compressor?
You will need an air compressor, a sandblasting gun, a media hopper, and abrasive media such as sand or glass beads.
How do you assemble a sandblaster with an air compressor?
Connect the sandblasting gun to the air compressor and attach the media hopper to the gun. Fill the hopper with abrasive media and adjust the air pressure to the desired level.
Can any air compressor be used for a sandblaster?
Ideally, the air compressor should have a high CFM rating and be able to deliver consistent pressure. A minimum of 7 CFM at 90 PSI is recommended for most sandblasting jobs.
What types of abrasive media can be used with a sandblaster?
Common types of media include sand, glass beads, aluminum oxide, walnut shells, and baking soda. The choice of media will depend on the surface being blasted and the desired finish.
Is it safe to use a sandblaster with an air compressor?
Sandblasting can be hazardous if proper safety precautions are not taken. Always wear protective gear such as gloves, a respirator, and eye protection. Work in a well-ventilated area and avoid exposure to the abrasive media.
How do you control the amount of abrasive media that is blasted onto a surface?
Adjust the air pressure and the size of the media nozzle to control the flow of abrasive. Start with a low pressure setting and gradually increase until the desired amount of media is being used.
What types of surfaces can be blasted with a sandblaster using an air compressor?
Sandblasting can be used on a variety of surfaces including metal, brick, concrete, and wood. However, it may not be suitable for delicate materials or surfaces that are easily damaged. Always test a small, inconspicuous area before blasting the entire surface.